Having worked with global players such as Anglo American and Glencore, Fuzzy Logic Studio is continuing to help those operating in the mining sector to unearth the potential of immersive technologies both above and below ground.
This cluster of technologies, which includes Augmented Reality (AR) and Virtual Reality (VR), has historically been associated with sectors such as retail, healthcare, and the military. Now though, the impact it's having on the mining sector is starting to garner more attention as companies across the supply chain look for tools to improve training, boost productivity, and enhance the customer experience.
Reducing Training Times
“Mining is a heavily regulated industry with stringent practices relating to training and onsite safety. One of the challenges though is that it isn’t always physically possible to replicate certain scenarios in real-life, due to the danger involved,” explains Jason Ried, Founder of Fuzzy Logic Studio.
Virtual Reality offers one way in which trainees can be safely immersed in potentially hazardous environments to put critical skills into practice. By testing users along the way, training managers can also ensure compliance with regulatory requirements and automatically gather data for accurate record keeping.
The value of Augmented Reality is found in the fact that it can enable large scale machinery to be brought into the training room. Accurate 3D models of the machinery can be placed in the physical environment, giving trainees the ability to interact and engage with both the external and internal components. This is often difficult to achieve, as it requires machines to be taken out of service for a period of time, resulting in downtime and potential revenue loss.
Visual step-by-step guides also present an opportunity to walk-through key processes and maintenance procedures, ensuring trainees are well-equipped with the skills they need in the field.
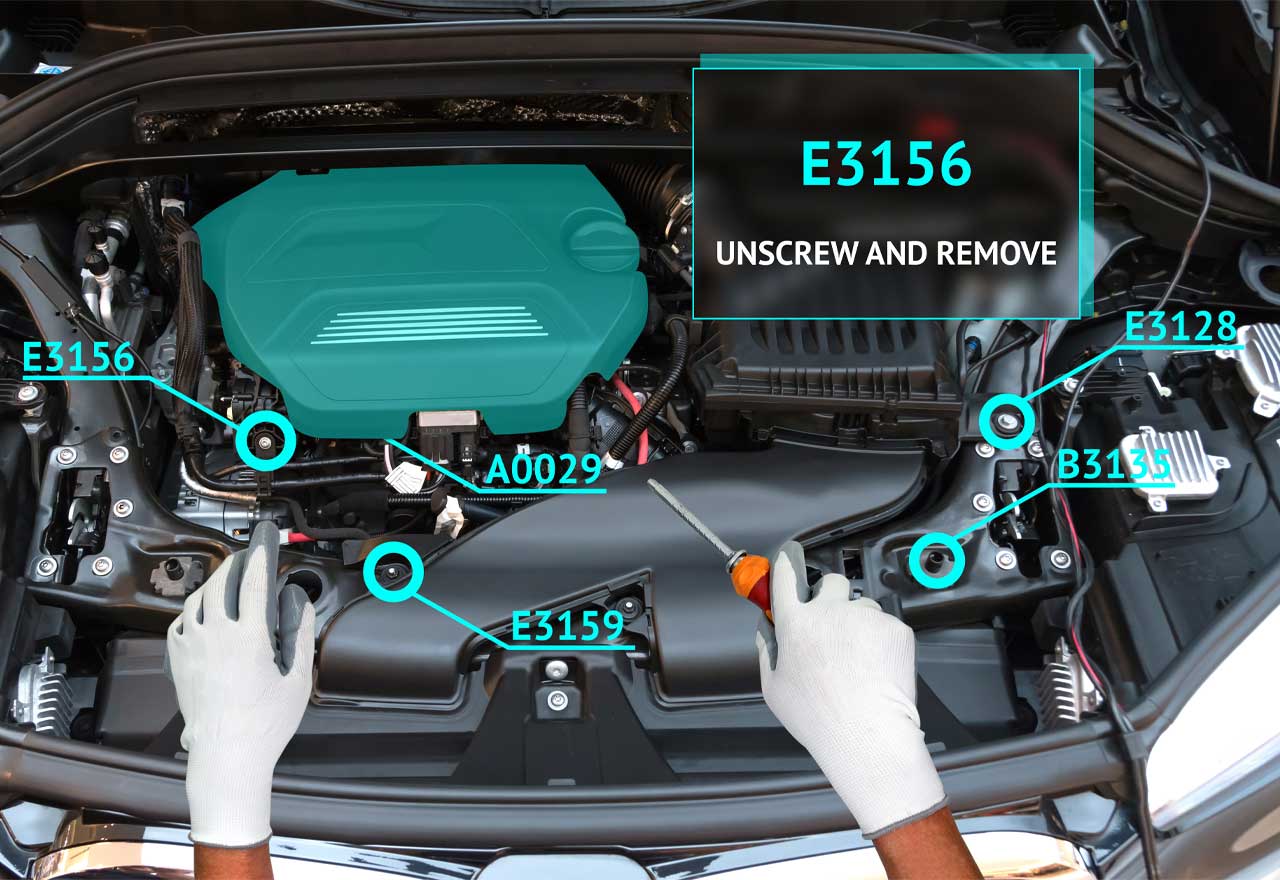
Ried adds: “Both Augmented Reality and Virtual Reality require users to actively participate in experiential learning. This has been scientifically proven to improve knowledge retention.”
Improving Productivity
Back out in the field, teams go through numerous processes each day. Some of these they may be familiar with, whereas others might be completely new. Augmented Reality can be applied in these instances to instruct and guide staff in real-time by overlaying step-by-step instructions onto a physical piece of equipment or a specific environment. This means staff can complete complex tasks efficiently and safely.
“Typically, paper-based checklists have been used to guide underground teams through processes. This leaves room for human error as stages can be accidentally missed, with the result being potential downtime or risk to safety. Digital checklists using AR reduce these risks as the system won’t allow them to miss out on any steps. The system can also be used to capture digital evidence that each process has been completed correctly,” says Ried.
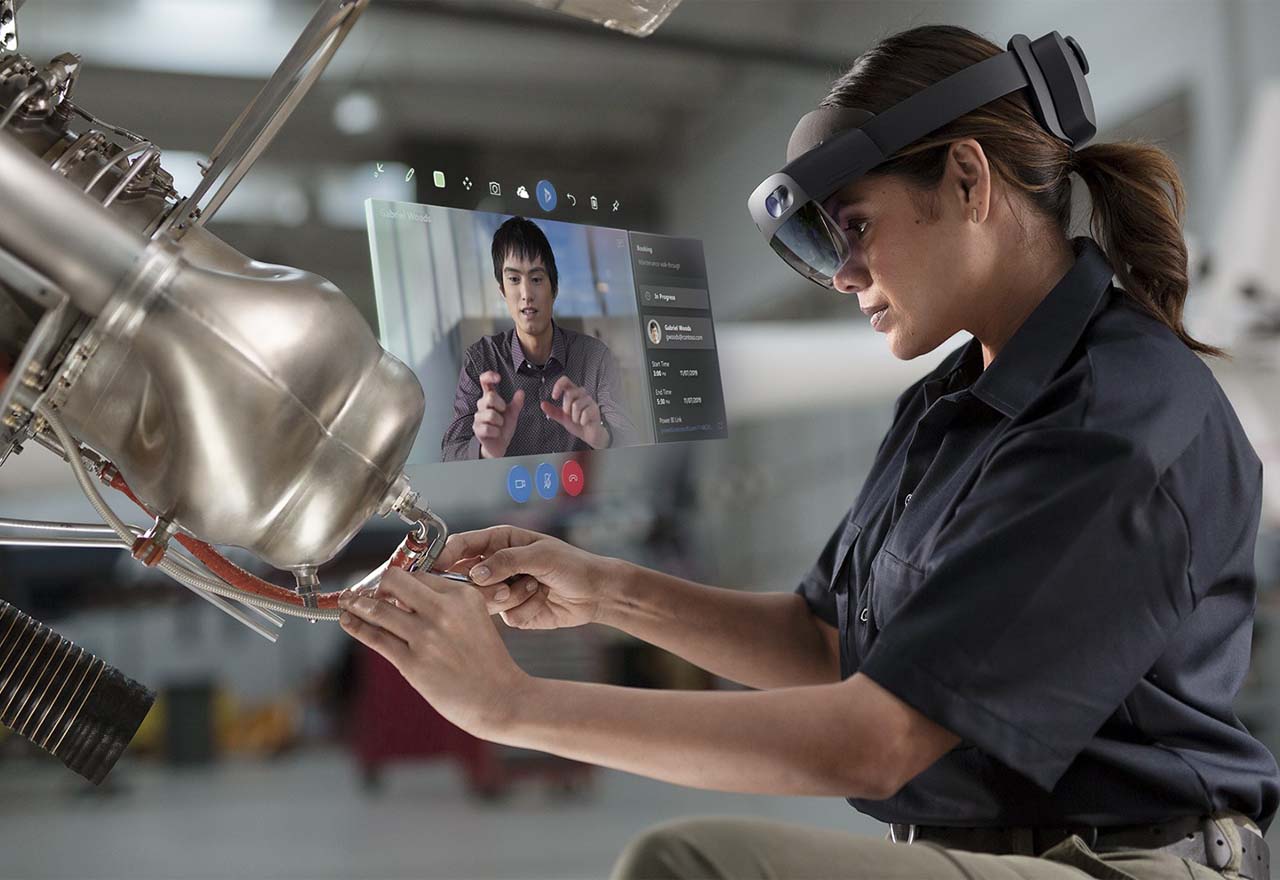
Even if a team member does come across a problem they can’t solve, augmented reality has the ability to connect them to the necessary support immediately. Across vast mining sites, it isn’t always possible to have more experienced technicians in the right place at the right time. The remote capabilities of augmented reality combine live video streaming with AR, so technicians can offer over-the-shoulder support wherever they are. This means they can directly see what the team member in the field is seeing and can draw into their field of view to guide them to a solution.
Driving Remote Sales
Ried explains: “With mines dispersed across the world, manufacturers and resellers of machinery in the industry often have team members on the ground to drive sales and ensure a high standard of after-sales service. This year, we’ve seen the impact it can have when companies aren’t able to physically interact with their customers and showcase their product offering at trade shows.”
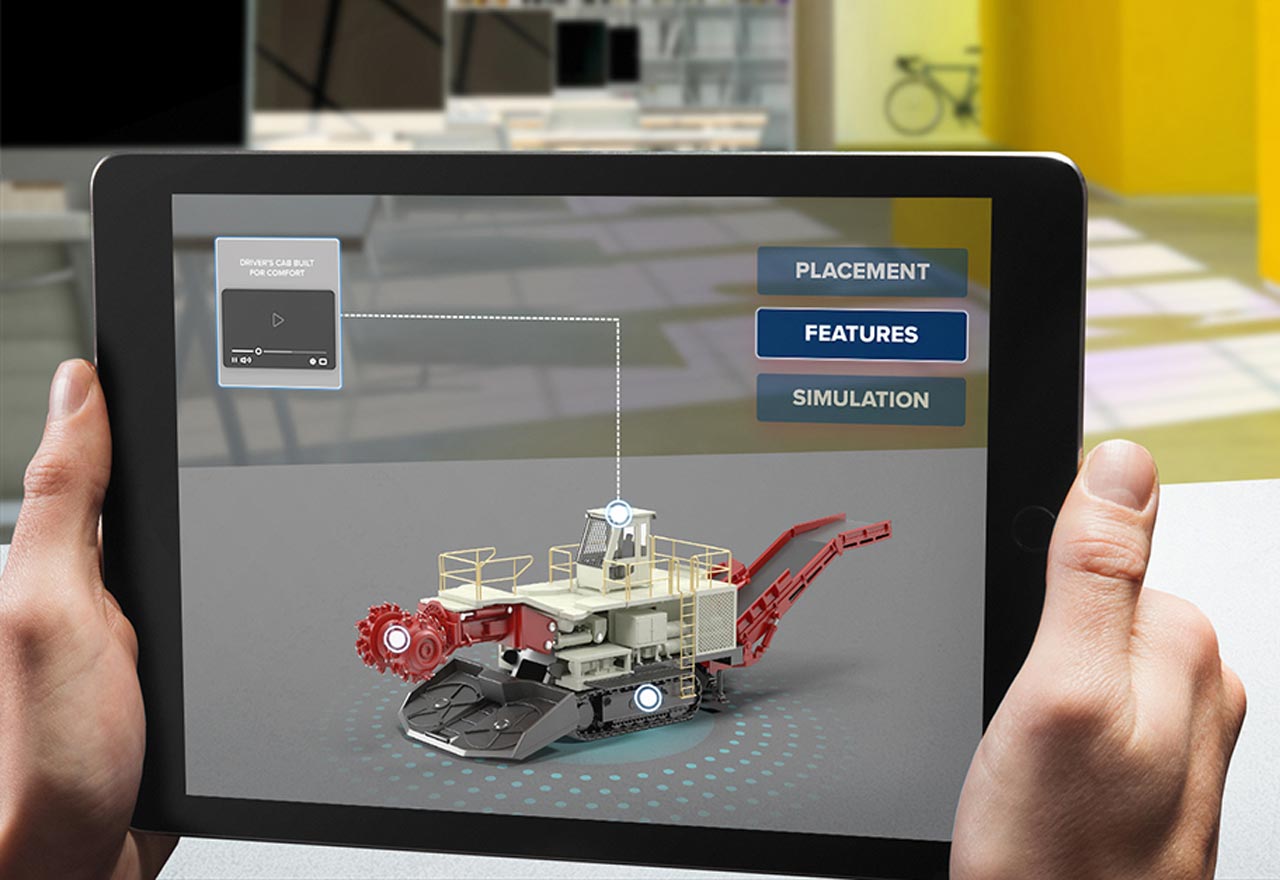
The benefit of augmented reality in the sales setting is that it can be used to facilitate remote digital product demonstrations. For example, a sales representative can position a realistic 3D replica of a machine into a customer’s work environment without needing to be physically present. Interactive touchpoints can then be tagged onto the model, highlighting specific selling points. This helps to overcome some of the challenges often encountered with traditional product demonstrations. AR sales tools can help customers to interact with products that may be too large to bring into particular environments or visualise key internal features or components that would typically be difficult to see otherwise.
“The customer journey doesn’t just end at the point of sale. In mining, it’s critical to a business’s success that the machinery remains operational. Rather than providing instruction manuals, suppliers can create digital maintenance tools using AR to guide customers through common maintenance processes. The remote assistance capabilities can again be applied in this context to connect customers to real-time support in the field. This helps businesses avoid periods of prolonged downtime and their suppliers to reduce travel costs for their experts”, adds Ried.
The Introduction of 5G
A recent development that will further accelerate the adoption of immersive technology is the rollout of 5G connectivity, both above and below ground. Now, more than ever, those operating in mining have an opportunity to lead the charge and blaze the trail for other industries to follow.